Pre-machined precision steel versus raw material
- Use the advantages and save costs!
Pre-machined precision steel is a workpiece that is machined on all sides with a guaranteed decarburised surface, which can be used directly for the manufacturing of industrial precision products. This material is also referred to as a semi-finished product as it represents the “halfway” point on the path to a finished component.
This can be precision flat steel as well as round steel with or without machning allowance.
A tool and die designer should plan for pre-machined steel (e.g. fine-milled or ground) rather than sawn raw material, as this offers several technical, economic and quality advantages that optimize the entire manufacturing process and minimize the risk of problems in later processing and hardening steps of the steel.
Our range of precision steels stands out for its extensive selection of dimensions, tightest tolerances, and exceptional surface quality.
We are your reliable partner for precision flat steel, precision round steel, precision P-plates, and €co-Präz bars.
PREMIUM Steel in 70 grades and 36.234 dimensions.
Ex works from our warehouse –
short delivery times
We are happy to advise you!
Custom dimensions on request – sawn – milled – ground.
A basic consideration for a designer when choosing between pre-machined precision steel and raw (unmachined) material.
When manufacturing a precision steel component, the designer must first decide which type of steel meets the required technical specifications. Once this choice is made, the next step is to determine which material best fulfills the demands for dimensional accuracy, surface quality, and cost-effectiveness.
The choice of material significantly influences the manufacturing effort, production time, and overall costs. The following aspects should be considered when selecting pre-machined steel:
ACCURACY OF THE RAW MATERIAL
How precisely does the raw material already match the desired final dimensions?
MACHINING EFFORT
How many processing steps are required to bring the steel to its final dimensions?
COST FACTOR
How do material costs, processing time, and machine usage impact the overall costs?
Graphic representation: Decision-making process for the selection of the starting material
A: SELECTION OF
STEEL GRADE
1.XXXX
Objective after hardening:
High working hardness
High tensile strength
B: SELECTION OF
HARDENING PROCESS
Volume hardening
Surface hardening
Volume and surface hardening
C: CHOICE OF
STEEL PURCHASE
Precision steel
WITHOUT machining allowance
Precision steel
WITH machining allowance
Raw material / saw cut
The following table shows the three different specifications of materials which can be used to manufacture precision work pieces from tool steel or corrosion resistant steel and the appropriate hardening processes.
Precision flat steel WITHOUT machining allowance |
Precision flat steel WITH machining allowance |
Sawn raw material |
---|---|---|
Finishing dimensions of the starting material (mm): 100,0 x 20,0 x 500 |
Finishing dimensions of the starting material (mm): 100,3 x 20,3 x 500 |
Finishing dimensions of the starting material (mm): 105 x 25 x 505 |
Accuracy: Very high (most precise pre-material) |
Accuracy: High (true to size, but reworking necessary) |
Accuracy: Low (rough finish) |
Processing efforts: No post-processing required; can be used immediately |
Processing efforts: Grinding/milling required to achieve final dimensions |
Processing efforts: Extensive processing required (milling, grinding) |
Intended Use: • Precision components • tight tolerances • no follow-up work |
Intended Use: • Precision components with standardized follow-up work |
Intended Use: • Rough components • cost-conscious production • high volume of follow-up work |
Suitable hardening processes: • Vacuum hardening • nitriding • plasma nitriding • laser hardening • induction hardening |
Suitable hardening processes: • Conventional hardening • case hardening • flame hardening • hardening in liquid media |
Suitable hardening processes: All the options for hardening processes as before |
Precision flat steel
WITHOUT machining allowance
Finishing dimensions of the starting material (mm):
100,0 x 20,0 x 500
Accuracy:
Very high
(most precise pre-material)
Processing efforts:
No post-processing required; can be used immediately
Intended Use:
• precision components
• tight tolerances
• no follow-up work
Suitable hardening processes:
• vacuum hardening
• nitriding
• plasma nitriding
• laser hardening
• induction hardening
Precision flat steel
WITH machining allowance
Finishing dimensions of the starting material (mm):
100,3 x 20,3 x 500
Accuracy:
High (true to size, but reworking necessary)
Processing efforts:
Grinding/milling required to achieve final dimensions
Intended Use:
Precision components with standardized follow-up work
Suitable hardening processes:
• Conventional hardening
• case hardening
• flame hardening
• hardening in liquid media
Sawn raw material
Finishing dimensions of the starting material(mm):
105 x 25 x 505
Accuracy:
Low (rough finish)
Processing efforts:
Extensive processing required (milling, grinding)
Intended Use:
• rough components
• cost-conscious production
• high volume of follow-up work
Suitable hardening processes:
All the options for hardening processes as before
Differentiation of the starting material:
Precision flat steel WITHOUT machining allowance: |
Precision ground flat steel WITH machining allowance: |
Raw material in the form of sawn sections: |
---|---|---|
Highly precise starting material, directly suitable for finishing. | True to size, but with allowances (typically +0,3 mm) to allow for post-processing by grinding/milling. | Coarse finish with large dimensional deviations and surface roughness. |
No additional material allowance necessary, as the surface is already dimensionally accurate and of high quality. | Suitable for components where decarburisation and warping of the workpiece is to be expected, e.g. due to a planned hardening process (e.g. when hardening in a furnace under oxygen). Here, further processing is necessary to achieve surfaces free of decarburisation and perfect dimensional accuracy. | Requires intensive processing (e.g. milling, grinding) to achieve the finished dimension. |
Ideal for precision components with close tolerances and minimal machining. Ideal for hardening processes where no surface decarburization or distortion of the workpiece is to be expected (e.g. vacuum hardening) |
Economical for components with low precision requirements or for the direct finishing of large components in a single clamping. |
Differentiation of the starting material:
Precision flat steel WITHOUT machining allowance:
Highly precise starting material, directly suitable for finishing.
No additional material allowance necessary, as the surface is already dimensionally accurate and of high quality.
Ideal for precision components with close tolerances and minimal machining.
Ideal for hardening processes where no surface decarburization or distortion of the workpiece is to be expected (e.g. vacuum hardening)
Precision ground flat steel WITH machining allowance:
- True to size, but with allowances (typically +0,3 mm) to allow for post-processing by grinding/milling.
- Suitable for components where decarburisation and warping of the workpiece is to be expected, e.g. due to a planned hardening process (e.g. when hardening in a furnace under oxygen). Here, further processing is necessary to achieve surfaces free of decarburisation and perfect dimensional accuracy.
Raw material in the form of sawn sections:
Coarse finish with large dimensional deviations and surface roughness.
Requires intensive processing (e.g. milling, grinding) to achieve the finished dimension.
Economical for components with low precision requirements or for the direct finishing of large components in a single clamping.
Do you have a question for us?
We are happy to advise you!
Precision flat steel
Precision round steel
Precision P-Plates
Pre-machined precision steel has its technical advantages

More precise dimensional stability
Pre-machined steel (precision flat steel, €co-Präz flat steel, precision round steel) has tighter tolerances when it comes to shape and size, which facilitates subsequent processing steps.
Sawn material requires additional processing (e.g. planing, grinding or milling) to achieve the desired dimensions and surface quality.
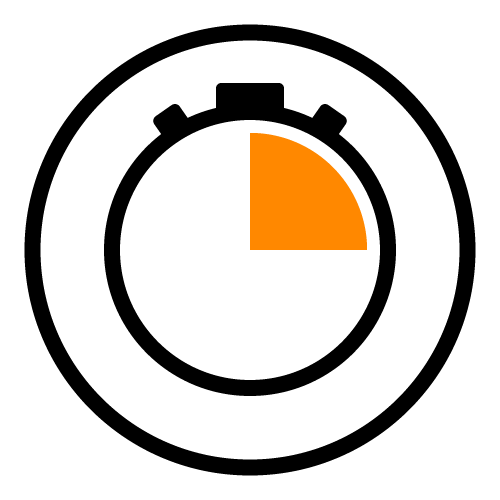
Less machining time
Pre-machined materials need less post-processing as the dimensions and the surface quality are already optimised.
Sawn material requires additional processing (e.g. planing, grinding or milling) to achieve the desired dimensions and surface quality.
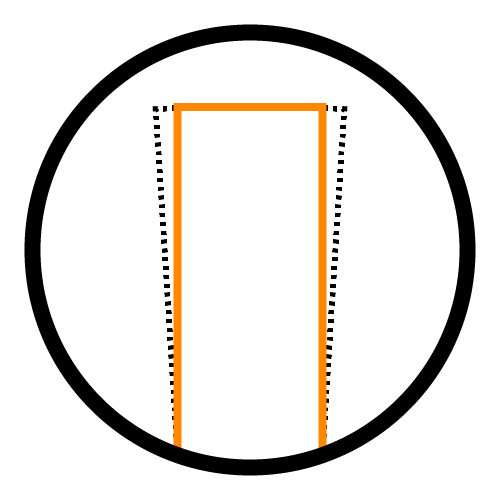
Reduction of machining and hardening distortion
When it comes to pre-machined steel, in particular finely milled or ground steel, we ensure that we use low-tension primary material and consistent machining, and we straighten components using roller straightening machines if necessary. This means that our steel has less internal stresses.
Sawn raw material, e.g. from rolled sheets or bars, has a tendency towards greater distortion due to inhomogeneous stress distribution during further processing and hardening.
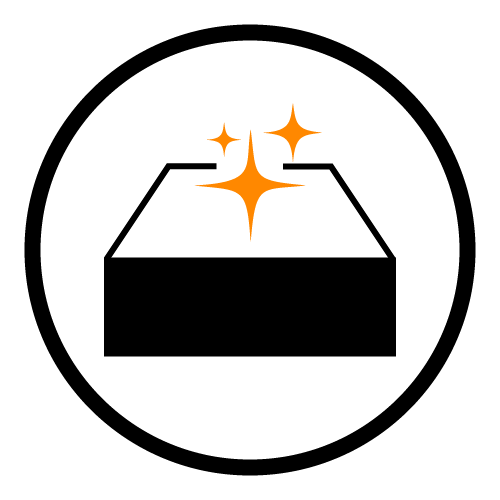
Improved surface quality
Fine-milled or ground surfaces are smooth and have a uniform structure, which is important for subsequent hardening processes (e.g. nitriding).
Sawn surfaces are often rough and irregular, which can make it difficult for carbon or nitrogen to diffuse in processes such as case hardening or nitriding.
Economic advantages of premachined precision steel
Cost savings for operational costs | Reduced material wastage | Faster turnaround time |
---|---|---|
Pre-machined steel reduces the need for rough or intermediatemachining, which saves machining time, tools and labour costs . | Pre-machined precision steel is already optimised to the required dimensions, which means that less material is lost through removal (e.g. during milling). | Since fewer processing steps are required, the manufacturing process is faster and more effi cient with pre-machined steel. |
For sawing raw material, all surfaces must be carefully machined fi rst before precise shapes or tolerances can be achieved. | Sawn material often has 5-10 mm excess width, thickness and length, which causes more material waste. | Sawn material extends the process chain due to the need for rough and intermediate processing. |
Economic advantages of premachined precision steel
Cost savings for operational costs
- Pre-machined steel reduces the need for rough or intermediate machining, which saves machining time, tools and labour costs.
- For sawing raw material, all surfaces must be carefully machined first before precise shapes or tolerances can be achieved.
Reduced material wastage
Pre-machined precision steel is already optimised to the required dimensions, which means that less material is lost through removal (e.g. during milling).
Sawn material often has 5-10 mm excess width, thickness and length, which causes more material waste.
Faster turnaround time
- Since fewer processing steps are required, the manufacturing process is faster and more efficient with pre-machined steel.
- Sawn material extends the process chain due to the need for rough and intermediate processing.
Quality advatages of pre-machined precision steel
Improved surface structure for subsequent processes
A smooth, pre-machined surface is ideal for:
- hardening processes such as nitriding and case hardening, as the diff usion of nitrogen or carbon is more even.
- clamping and assembly processes that require a high surface quality.
Sawn surfaces can have scratches or roughness that require reworking. As work pieces are unangular clamping can be diffi cult and unsafe.
Less internal stresses
Pre-processed steel is often made from raw material that has been specifi cally stress-relieved to avoid internal stresses prior to initial processing.
Sawn raw steel can have uneven stresses that cause problems such as warping, cracks or dimensional deviations during processing or hardening.
Homogeneity of the material
Due to the very fi ne surface, rare material defects (e.g. cavities, cracks) can be easily detected in pre-machined steel.
Such visual inspection is hardly possible with sawn raw material, which is why such material defects can only be detected much later after extensive processing, or even result in the risk of failure of the fi nished component.
Precise advantages of pre-machined steel in construction (planning of a component) and production (realisation of a precision component)
Designing on the basis of standardised precision steels (semi-finished products)
With pre-machined steel that is subject to DIN 59350, for example, in terms of its dimensions and tolerances, a designer can ensure that the component has more precise dimensions from the outset, which can significantly reduce the need for rework such as milling and grinding.
These standardised products are available directly from stock in over 30,000 different items and can be combined in a modular fashion, like LEGO building blocks.
Reduction of post-processing
With pre-machined steel, an engineer can ensure that the part has more precise dimensions from the start, thus minimising the need for secondary operations such as milling and grinding.
Reliability of component functionality
More precise dimensions and better surfaces lead to higher functionality of the component, especially with regard to fittings or bearings.
Optimisation for hardening processes
Hardening processes like case hardening and nitriding benefit from smoother, even surfaces as can be found in pre-machined steels.
Sawn materials can result in uneven hardening depth or surface quality.
When does it make sence to use sawn raw material?
In exceptional cases, sawn raw material can be an option:

Coarse, less precise components
When dimensional accuracy and surface quality are not of primary importance.

Prototyping
For simple, one-off applications where low-cost raw material is used.

Cost aspect
When the lower price of the raw material justifies the additional processing costs.
Conclusion
Sawn raw material is only useful in exceptional cases, when high standards of precision, surface quality or production efficiency are not required. For precision components requiring high standards of efficiency and cost-effectiveness, precision ground flat steel WITHOUT machining allowance is the optimal choice, especially in case of subsequent hardening processes without decarburisation and risk of distortion (e.g. vacuum hardening).
A designer should plan for pre-machined steel for the following reasons:
Higher dimensional accuracy and surface quality, reducing the amount of machining and post-processing.
Lower risk of distortion and material defects, increasing process reliability during hardening and subsequent industrial use of the component.
Shorter lead times and lower overall costs, improving production efficiency.